<div>No Regrets – Sean Vevea’s Bagged & Body-Dropped 2002 Chevy 3500 Dually</div>
Picture this: a "Utility Yellow" Chevy 3500 stake-bed truck, formerly owned and operated by the Pennsylvania Department of Transportation. Imagine the neglect and rust you'd expect to find under and within it, thanks to a life lived hard and put away wet. Think of the "government fleet vehicle"-spec trim and complete lack of features of any kind, including a vinyl seat and vinyl flooring. It refuses to start without ether or compressed air in the fuel tank. You take it for a test drive, and it loading up on fuel and rolling coal, and won't seem to stop. The duct taped seat is pulling apart; you peel back the tape only to find a stuffed penguin propping the seat up where foam should have been... It's your dream truck, isn't it?
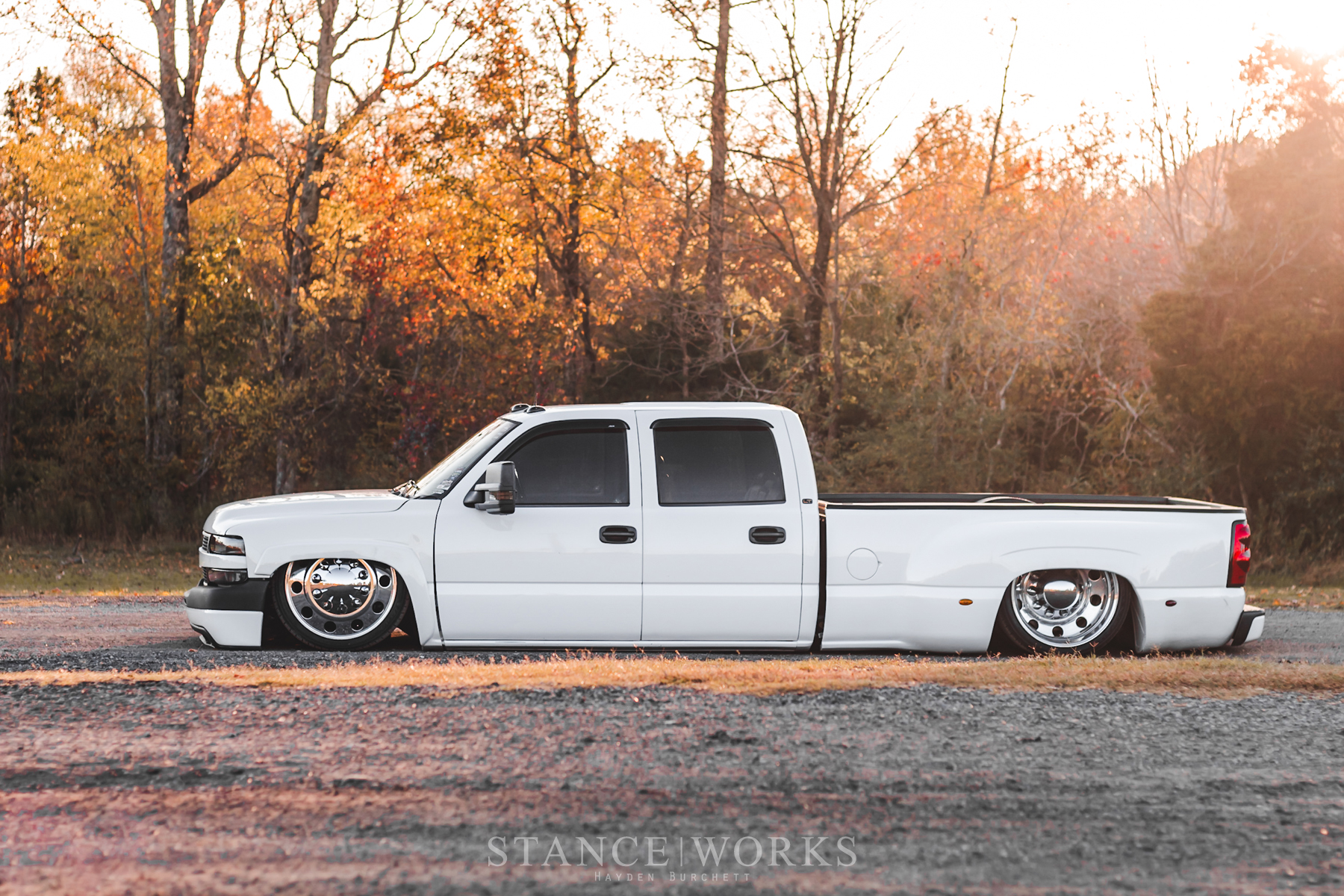
No? Well, the story differs for Sean Vevea of Nashville, Tennessee. In 2012, Sean found such a truck to be irresistible, and with it, kicked off a build that continues to this day, nearly nine years later. Although it wasn't until March of 2014 that progress began, it was a concept that had been with Sean for ages: a bagged and body-dropped dually proves too alluring for some to ignore. 24.5" Alcoa semi-truck wheels shoehorned underneath factory bodywork is a look we'd find impossible to disagree with, and thankfully, Sean saw treasure where others clearly would have found trash.
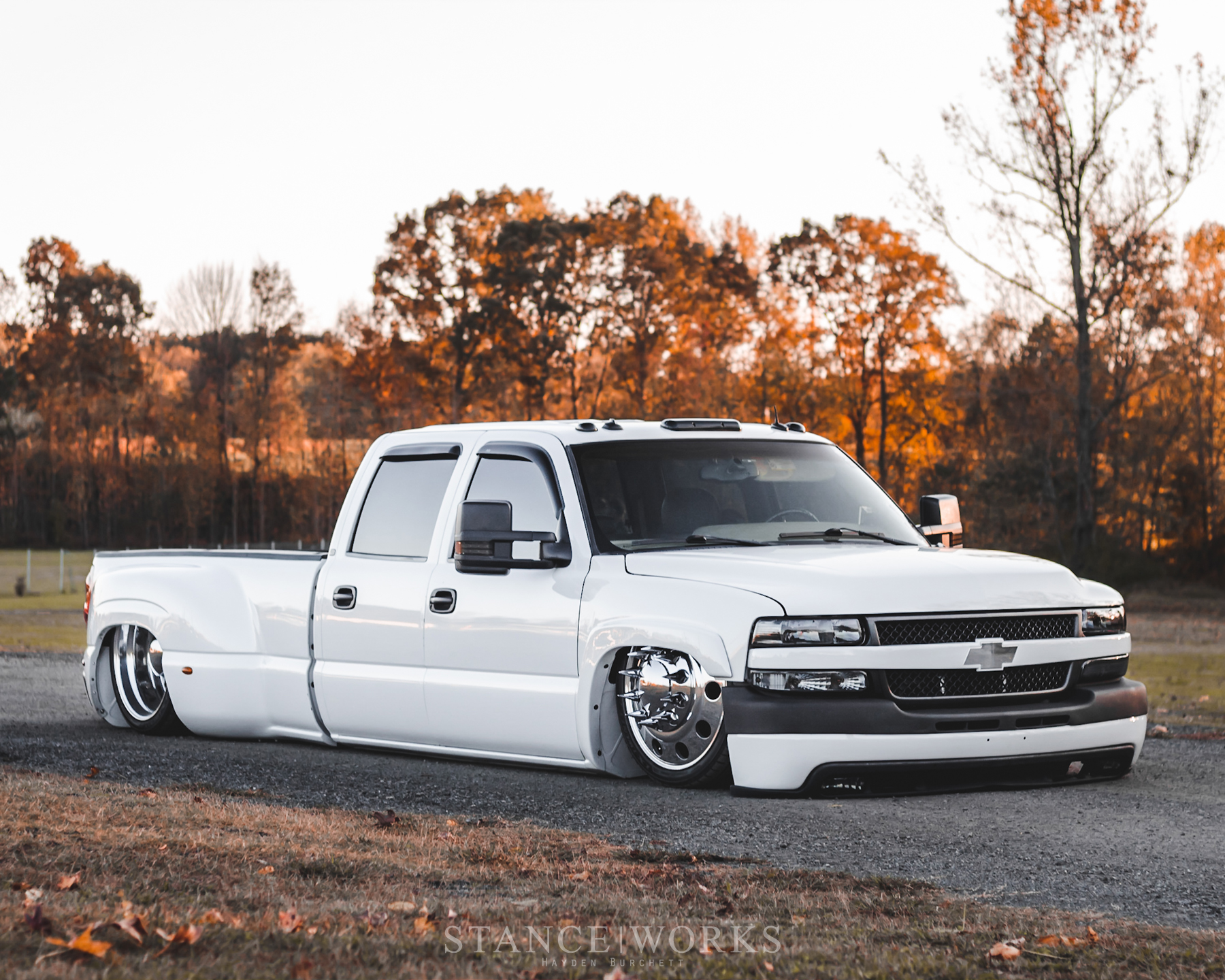
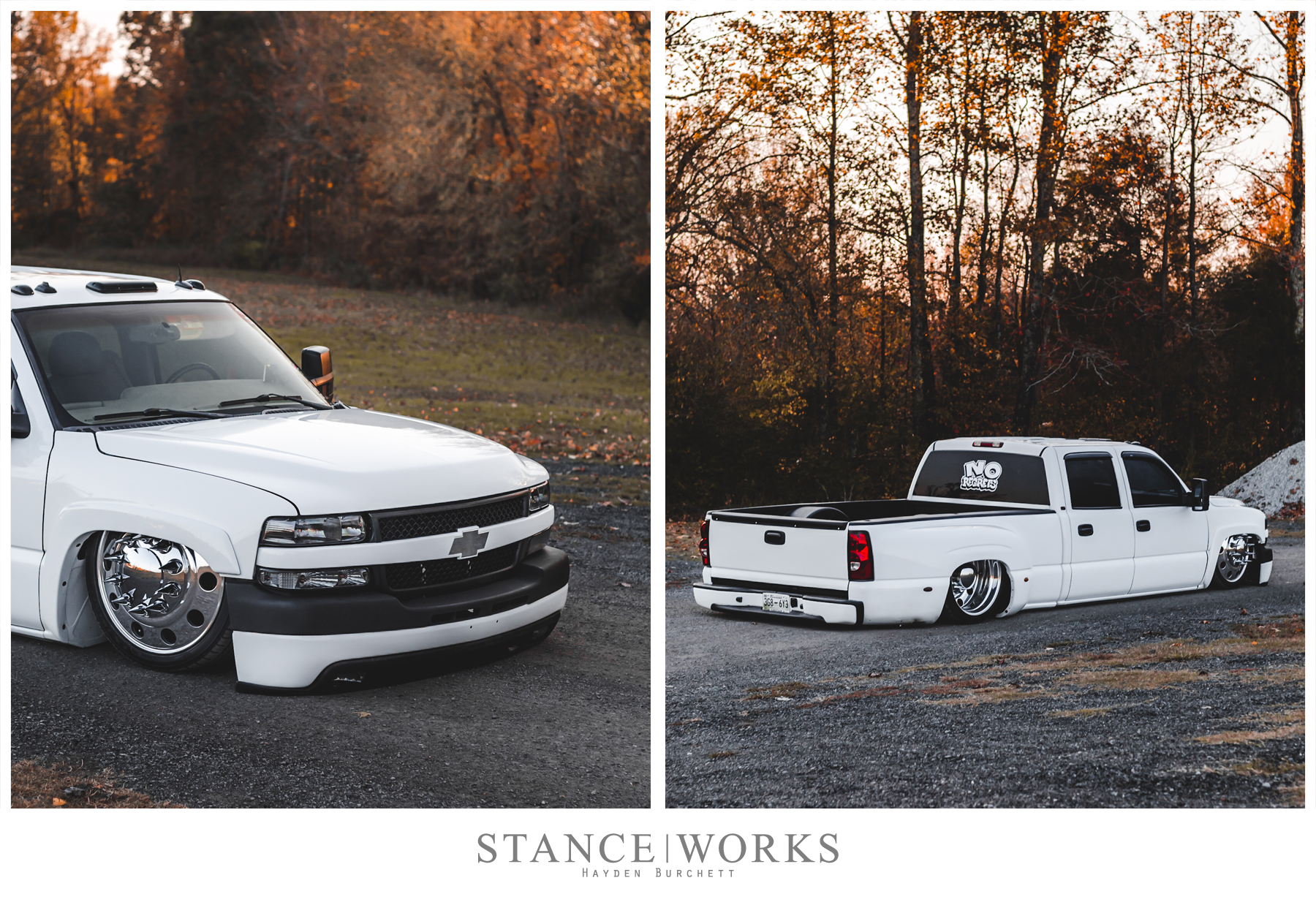
The beginnings of the build were admittedly a bit slow: not much headway was made in the first year or two. Once he acquired the Alcoa wheels, though, they began to turn, and momentum began to build. By May of 2014, Sean had installed a Little Shop MFG front control arm setup and air suspension at the nose of the 3500, along with the wheels, having turned them down to 24" and paired them with 24" Lexani tires. In July, a real teardown began: Sean removed the bed of the truck and, using an old Ekstensive 2-link kit, reconfigured the truck's rear suspension. The build utilized custom bridge and notch work to get the truck sitting low, and following that, the truck was driven around, fully bagged, for a few years.
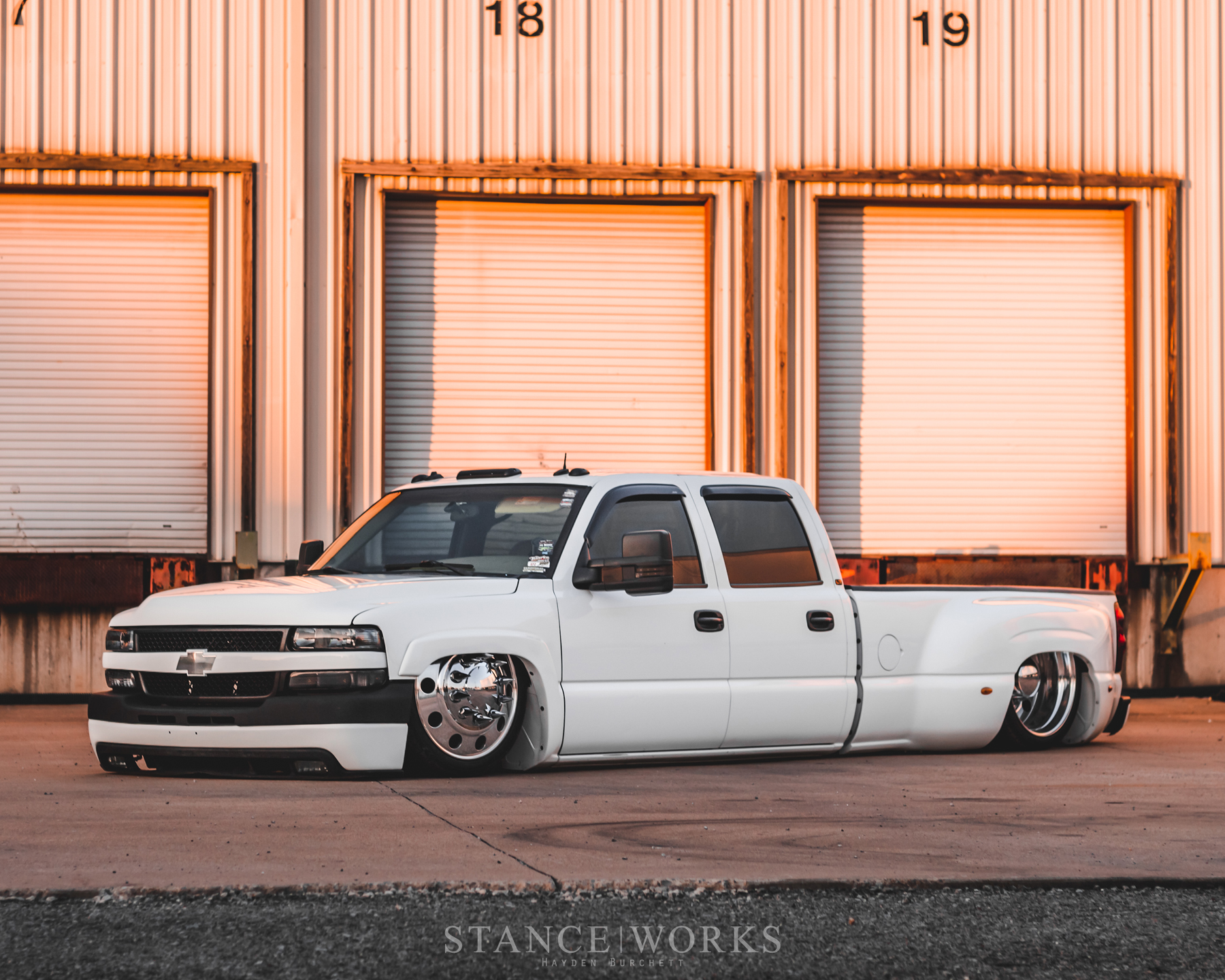
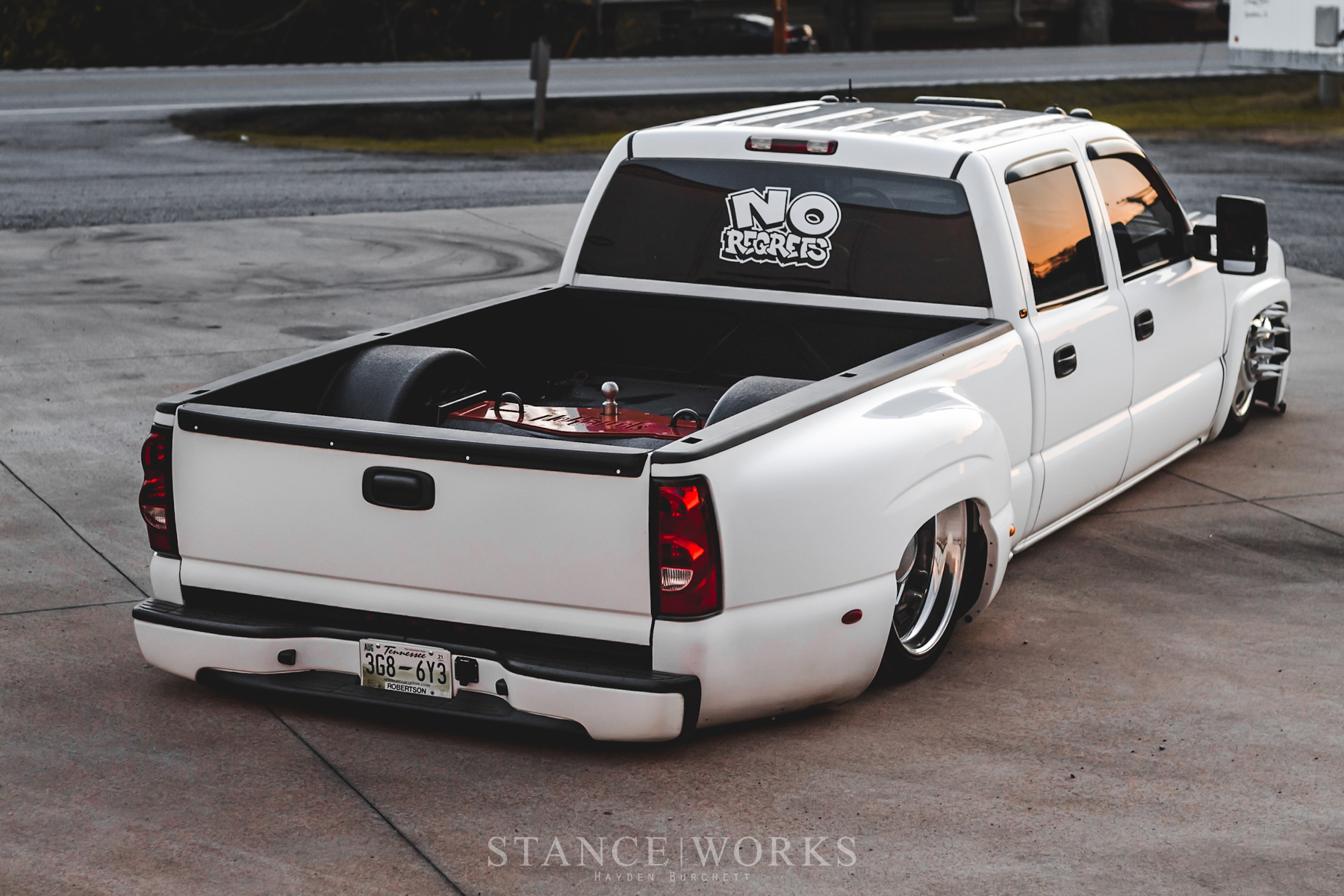
Eventually, though, it was envy that got the best of Sean. A Californian buddy with a body dropped Ford dually was clearly winning a non-existent competition, a feeling familiar to far too many of us. "It made me jealous," Sean says bluntly, but it was that sentiment that fueled a body drop of his own. A traditional 3" body drop along with cab mounts lowered another 2.5" lead to a loss of headroom inside the truck, but it was the best Sean could accomplish in his small home garage. The firewall was tubbed, the bed was redone, and the cab was cut... by September 2016, the truck was drivable once again.
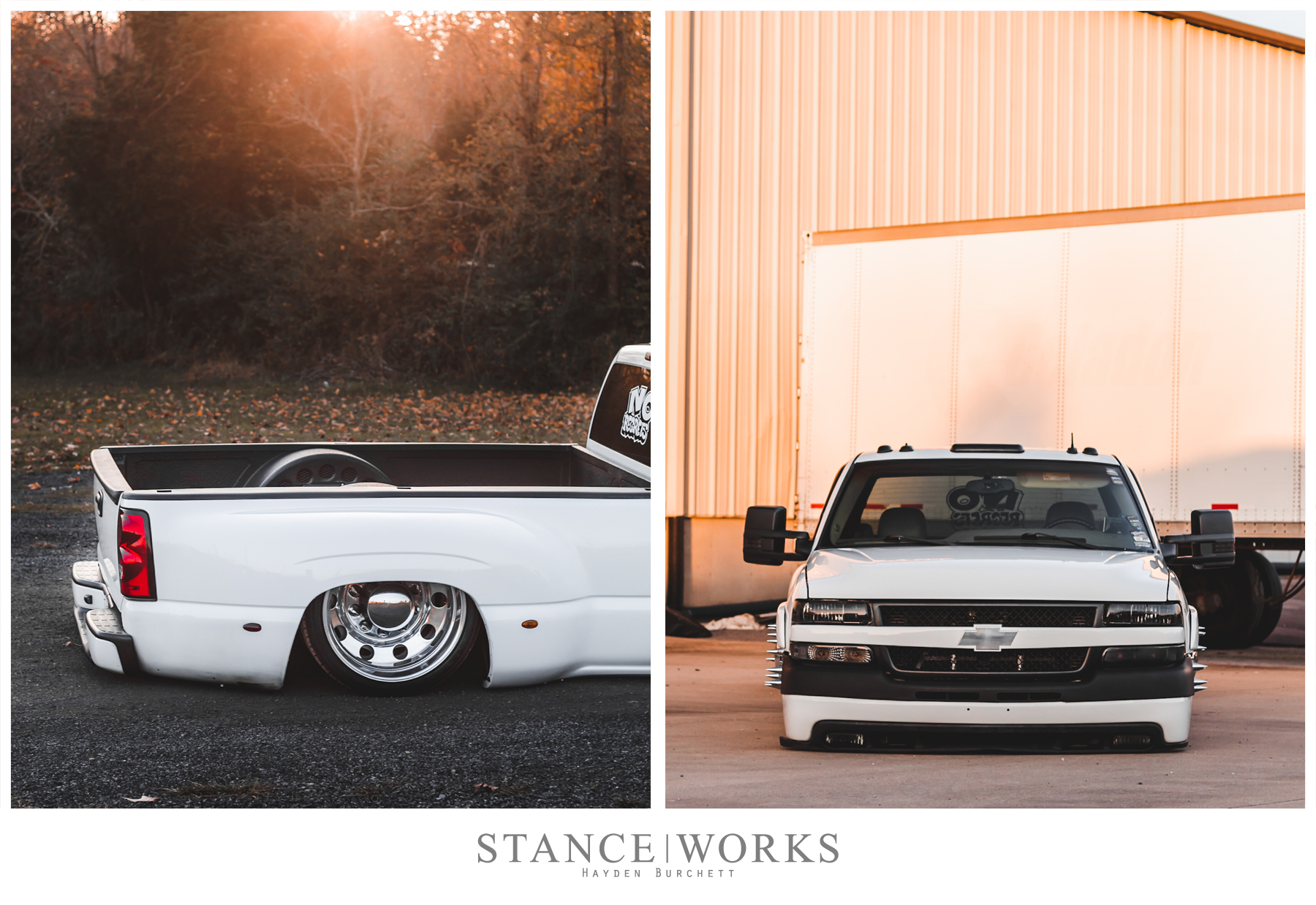
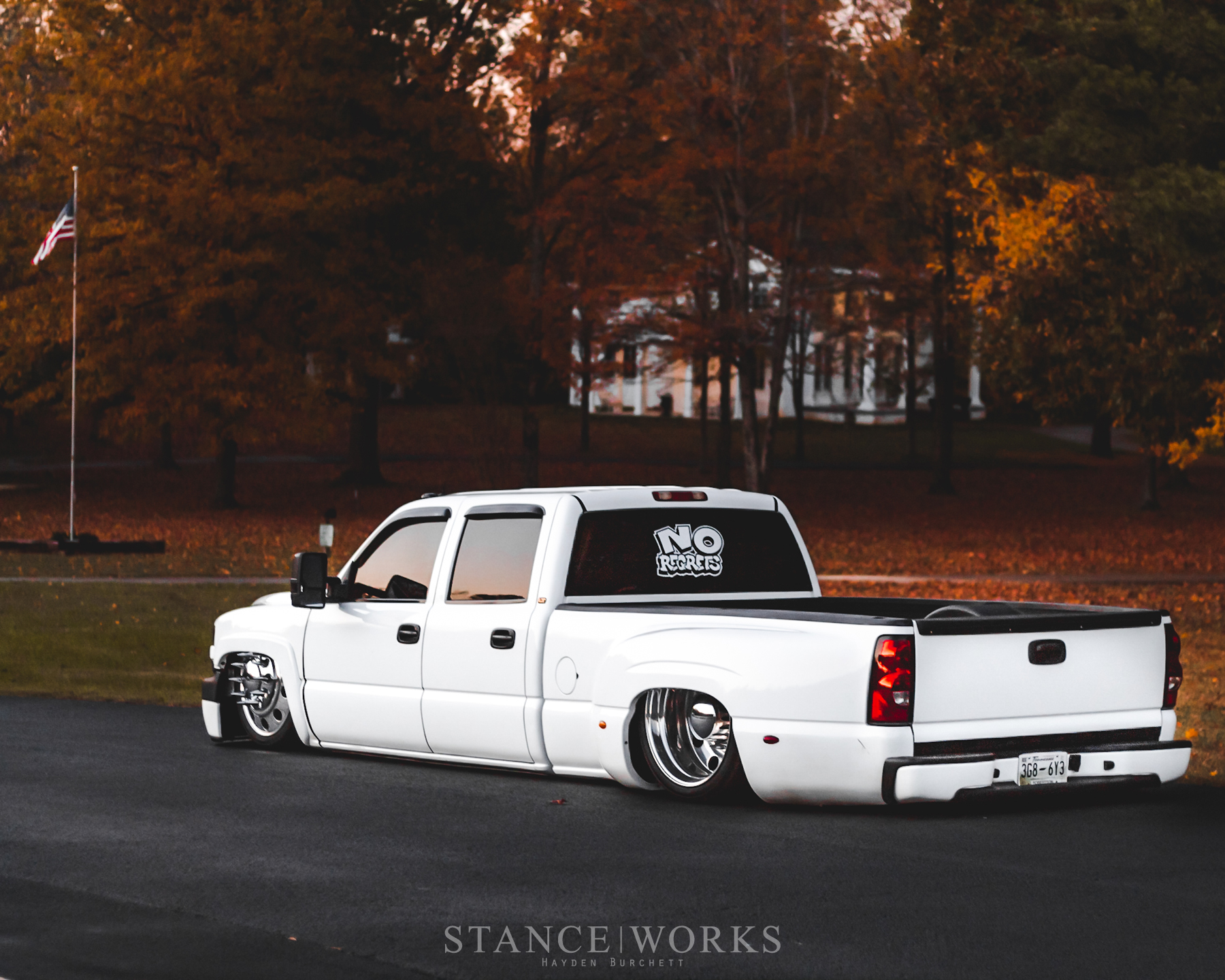
For most, that'd likely be enough, but Sean can't leave "enough" alone. In January of 2019, following a move to Nashville, he tore into the truck once again, this time to redo a significant portion of the work he had done prior, this time with a donor truck to solve the shortcomings. Using 2"x5" steel, he started the process by building a custom frame from the firewall to the rear notch, allowing the floor of his new donor cab to remain stock and retain as much headroom as possible. On the other hand, though, there was significant work to be done in order to keep the LB7 Duramax diesel from protruding through the hood. Custom mounts and oil pans, both upper and lower, moved the engine down an inch and a half, giving the necessary hood clearance. A custom transmission and driveshaft tunnel were fabbed up as well, allowing the whole system to clear, a hurdle he defines as perhaps the most challenging aspect of the build in its entirety. "Building it in a small 2 car garage, having to lift the cab off and on with an engine hoist and roll it around on dollies when it was in my way..." Sean explained the hurdles rather concisely: "There’s so many components to a common rail diesel truck that even though there’s seemingly a lot of room, there’s really no room at all."
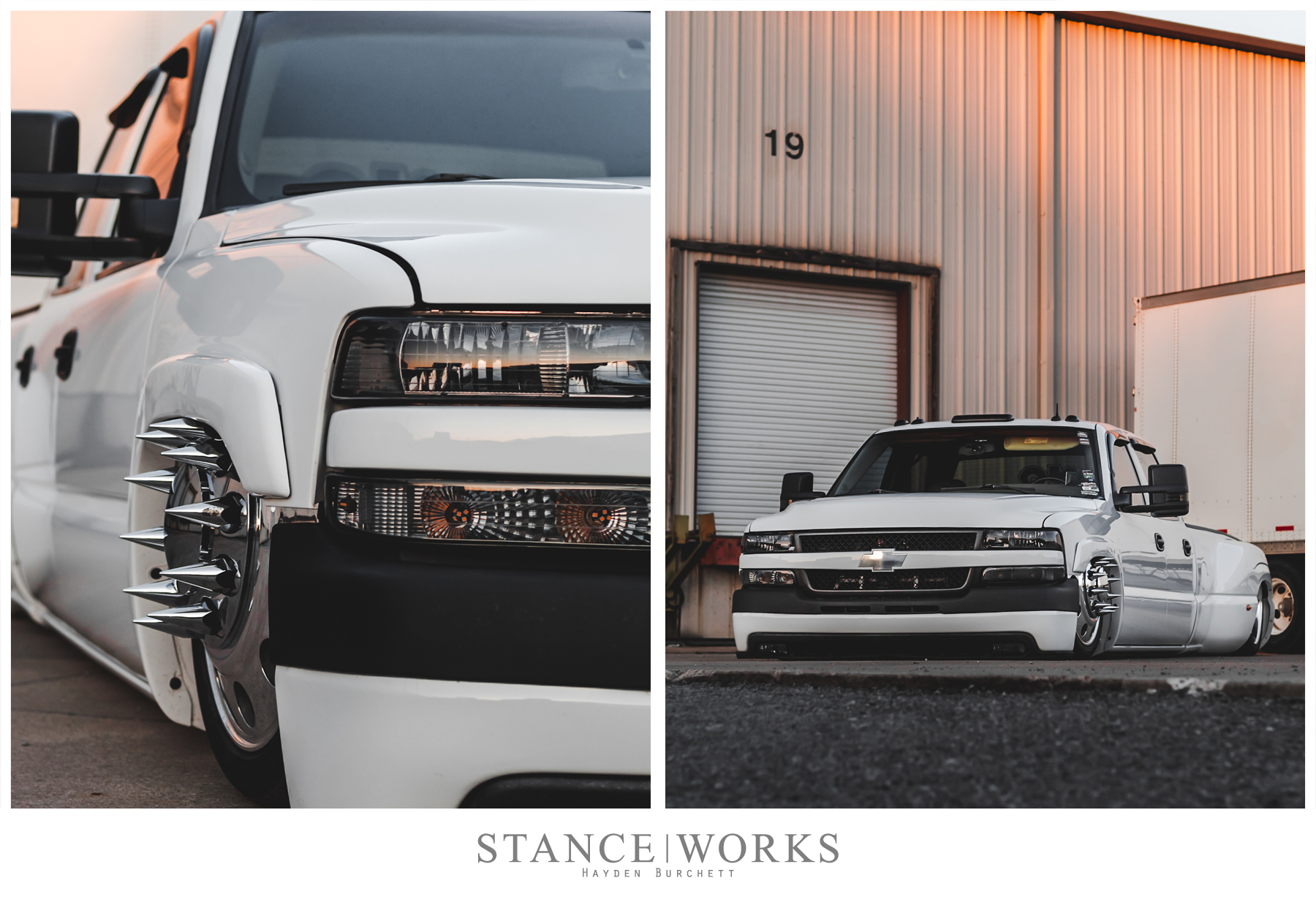
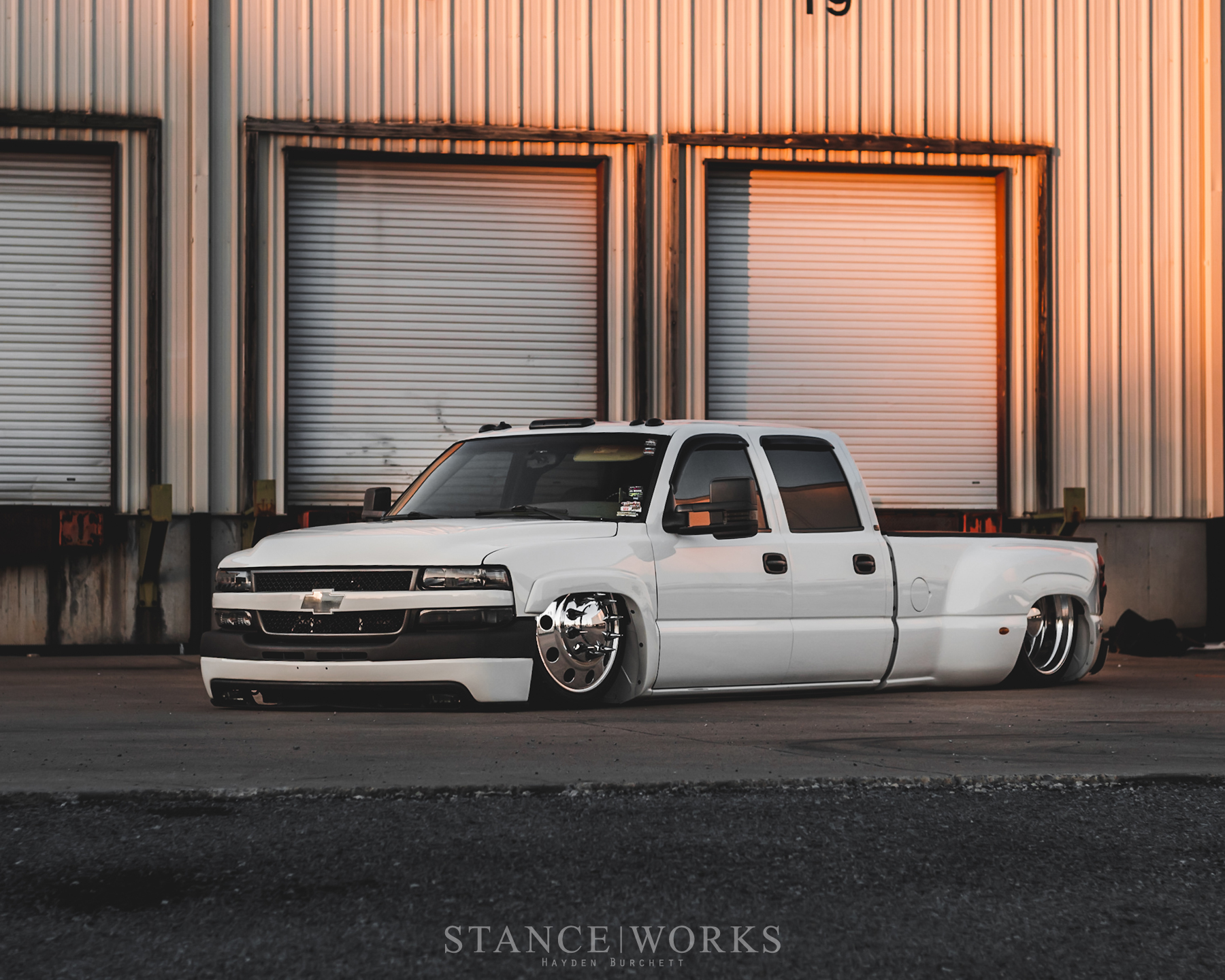
One of the major improvements done during the rebuild was a transplant of the body harness and the interior from Sean's 2003 LT-trim donor truck. The updated harness allowed for provisions such as power windows and locks, as well as luxuries like heated seats. Although the interior in the truck now is merely factory, the '03 LT guts are a significant improvement over the old and tired fleet truck innards the truck was originally equipped with.
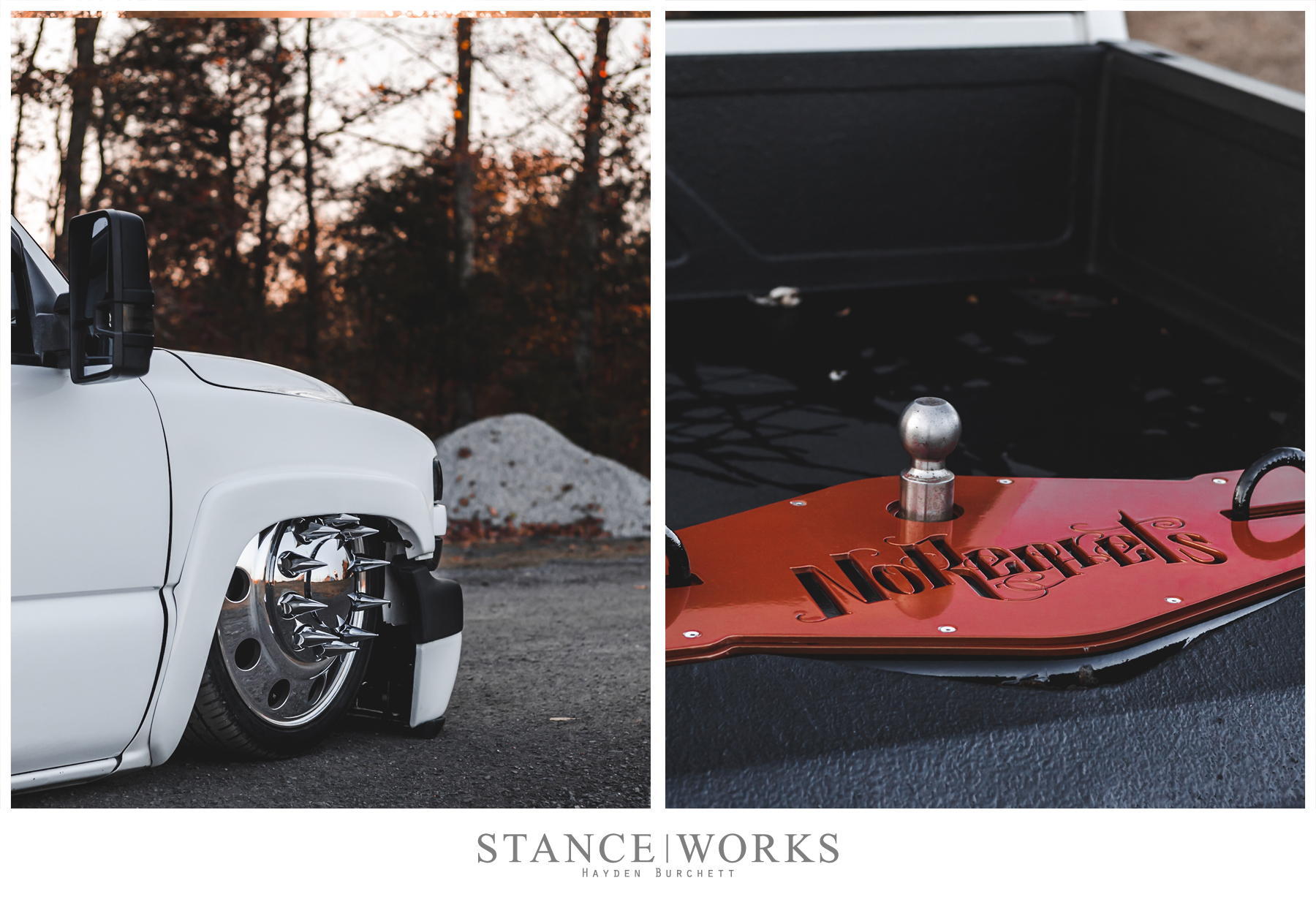
The rear end of the truck now utilizes a trailing arm setup, built by Sean himself. The arms span 56" and are built from cut and boxed 1/4" plate steel, and have been paired with a custom watts link and some frame work. The front end still sports the Little Shop kit, which features a custom tie rod setup, also built by Sean, to solve a common weak link area of similarly-built trucks. Air Lift Performance 3H management might just be the most technologically advanced part on the truck, with height sensors at all four corners for total digital control of the truck's overall stance and performance.
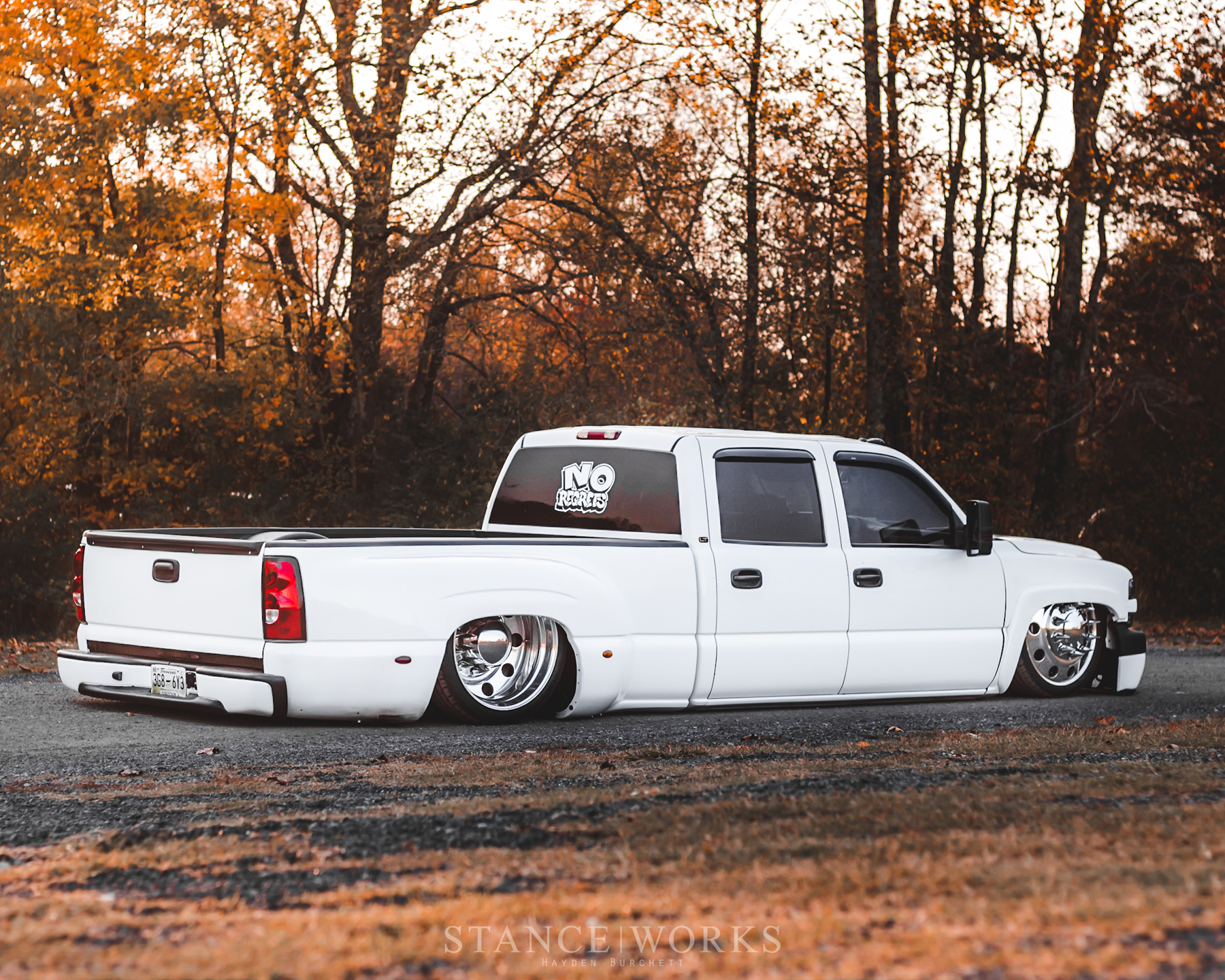
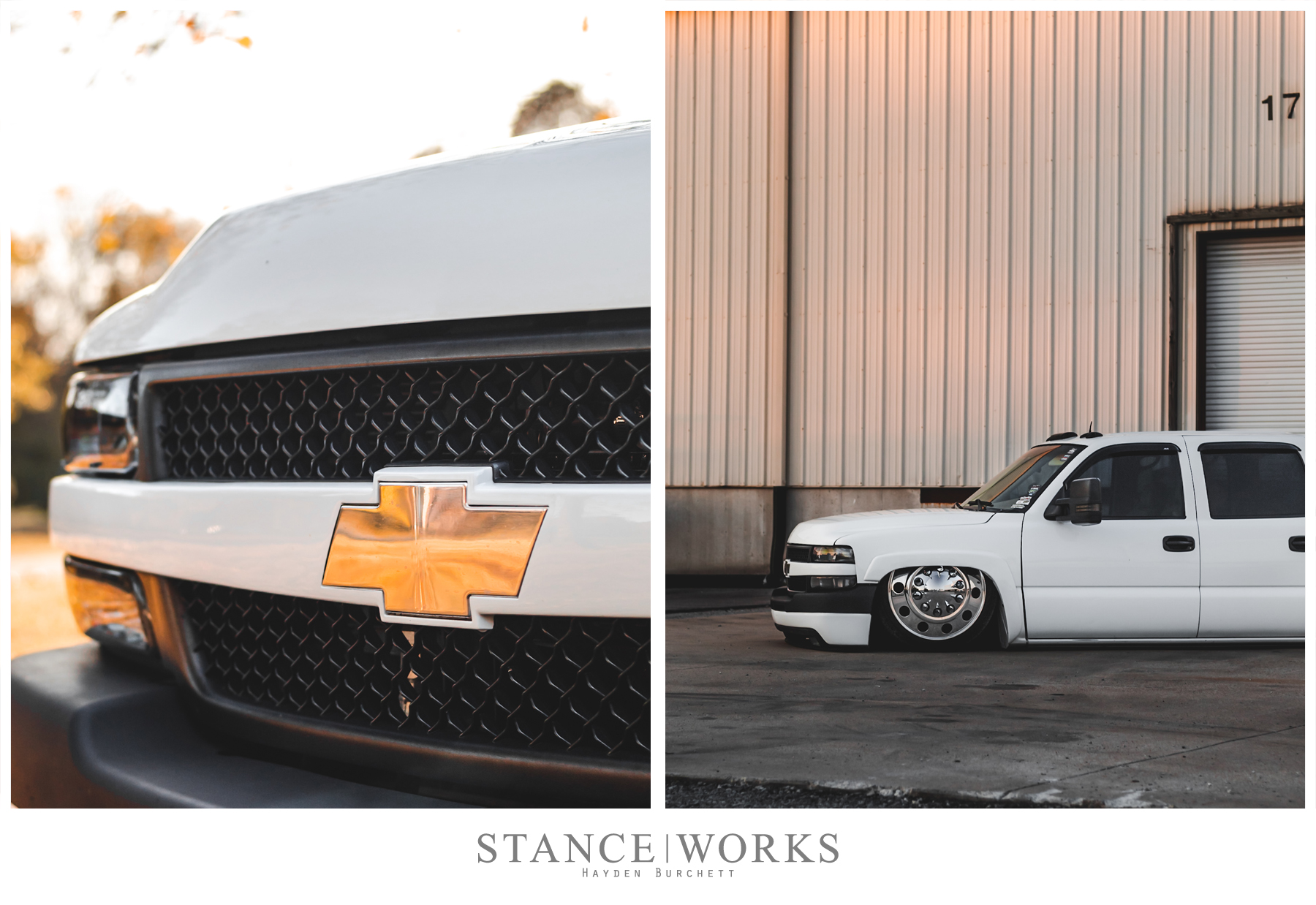
The truck's original yellow paint had been repainted green well before Sean's ownership, but with a white donor cab on hand, Sean began the process of hunting for white bed sides to match. The front clip, tail gate, and rear bumper we all eventually painted white too, yielding the incredible "white whale" Sean drives today, which brings us to 2020: Sean's truck, finally complete if only for the time being, is an incredible piece of machinery. With lug nuts that touch the fender arches, it's without question as good as a GMT800 gets. While he longs for a custom interior and another chance at custom paint, we're hopeful he's as happy with his own work as we are. If not, we're eager to see what comes next, but at worst, he can rest assured knowing his current point of progress in an ongoing build will undoubtedly inspire at least one future wrencher... and that makes it all worthwhile.
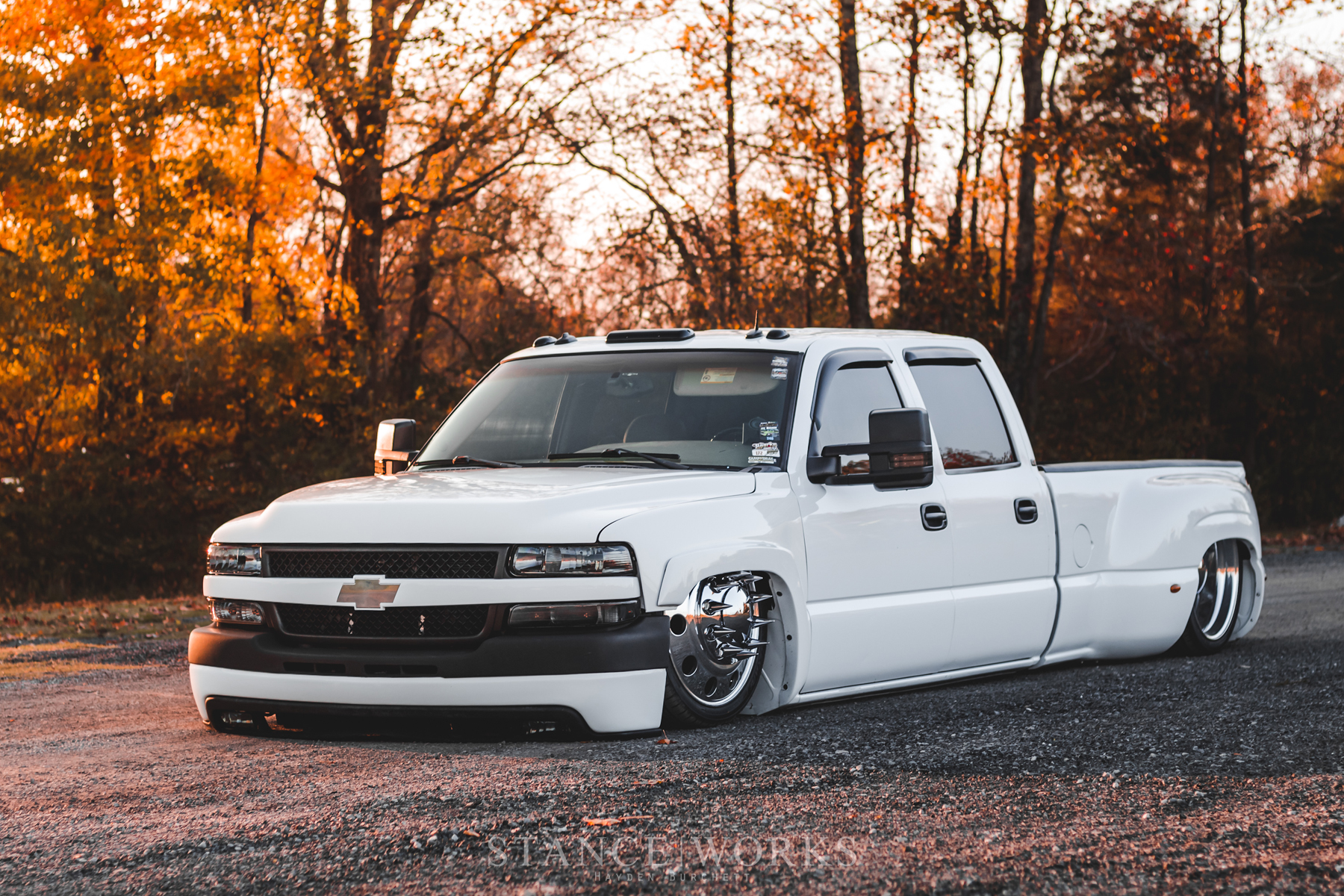